Ewellix launches new series of IoT-ready electro-mechanical actuators.
Ewellix, formerly SKF Motion Technologies, has developed the new actuators, which deliver forces up to 82kN and speeds of 1m per second, to provide real-time, accurate information that improves machine productivity.
With the newly designed Ewellix actuators, production line upgrades are now possible without major modification of existing machine layouts. The new CASM-100 and LEMC actuators feature integrated force sensors within the body of the actuator to provide a precise measurement of the torque being delivered from the motor through the internal ball or rollerscrew, even when the actuator is stationary. In addition, the sensor acts as a temperature monitoring device that activates an alarm if the actuator is at risk of overheating.
This configuration provides operational information in real-time, which can be communicated to higher level control systems. As a result, it is possible to improve overall performance and productivity, with greater safety.
Damien Ehry, Global Business Support Manager at Ewellix, says: “This is an exciting development for the CASM-100 and LEMC actuators. Both types of actuators are available in multiple combinations covering a wide range of applications which makes them particularly popular with manufacturers and design engineers. Increased accuracy, flexibility, high performance and reliability of these actuators all adds up to improved productivity and lower maintenance costs for our customers compared with traditional hydraulic systems.
“The built-in sensors improve on this further. Accurate measurements can highlight how space and energy savings can be achieved through downsizing attachments. This leads to an overall cost reduction of the production line, while still delivering safer manufacturing processes, demonstrating that Ewellix is developing IoT-ready technology with the customer in mind.”
A further advantage of having the Ewellix IoT-ready actuators with sensors is that when converting from a hydraulic system to an electro-mechanical one, it is easier to specify the correct sized actuator for the job. By using a prototype to replace one of the actuators before installing across the entire production line, manufacturers looking to switch to an electro-mechanical process can potentially benefit from even more cost, space and weight savings.
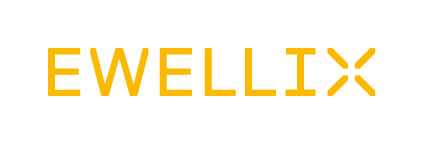