A shift to robotic welding processes to electric
One of the most significant advances in welding in recent years has been robotic or automated welding. Robotic welding workstations provide stable and higher quality welds and can improve work efficiency and reduce labour costs and dependency on skilled workers.
Partool, a specialist in building robots for welding setups based in Belgium, quickly realised that there was a massive shortage of this type of welder on the market. However, to automate welders, they were looking for a solution that could be easily programmed so that operators on the shop floor could do it autonomously and increase productivity.
70% to 80% increase in production output
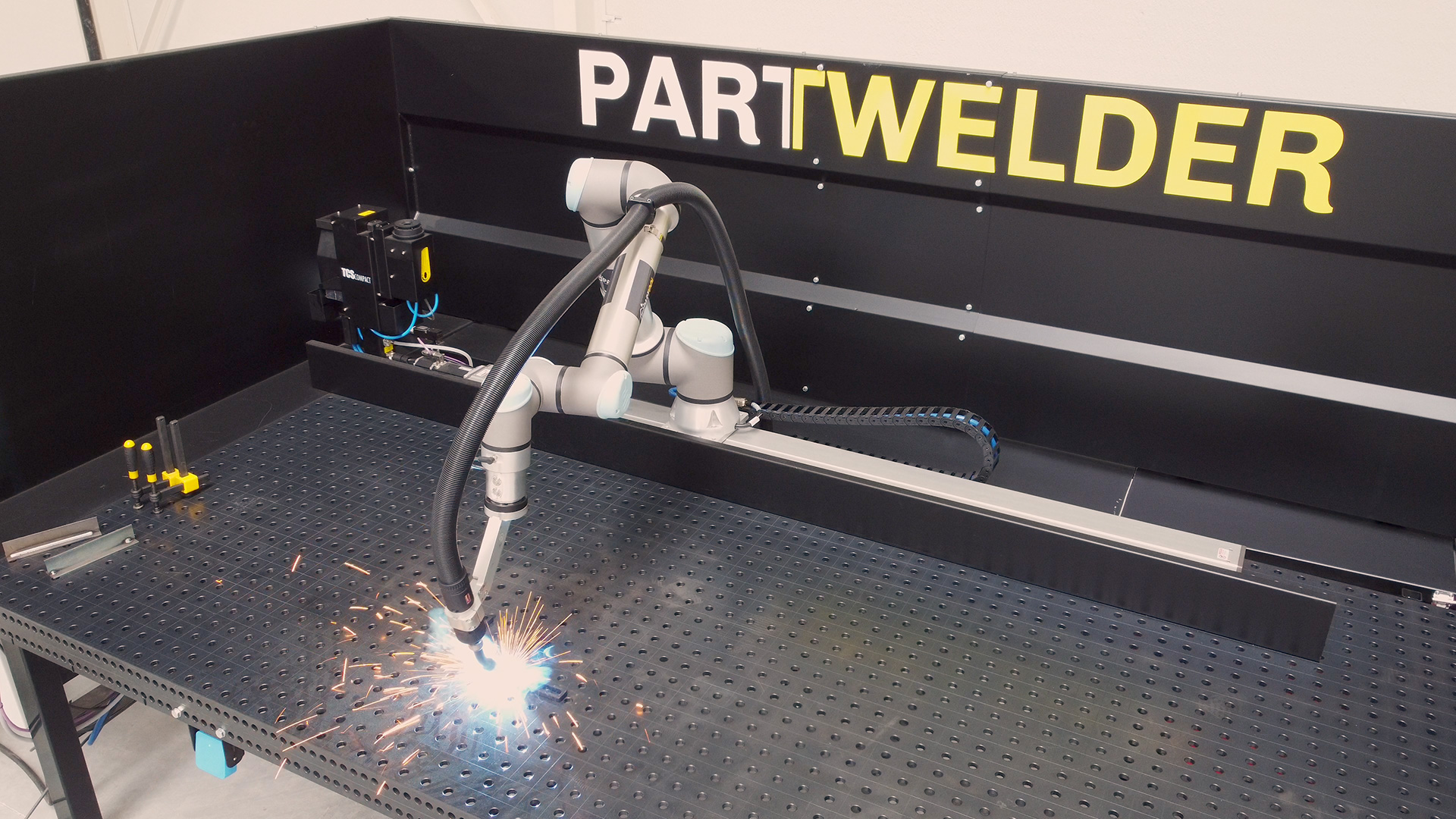
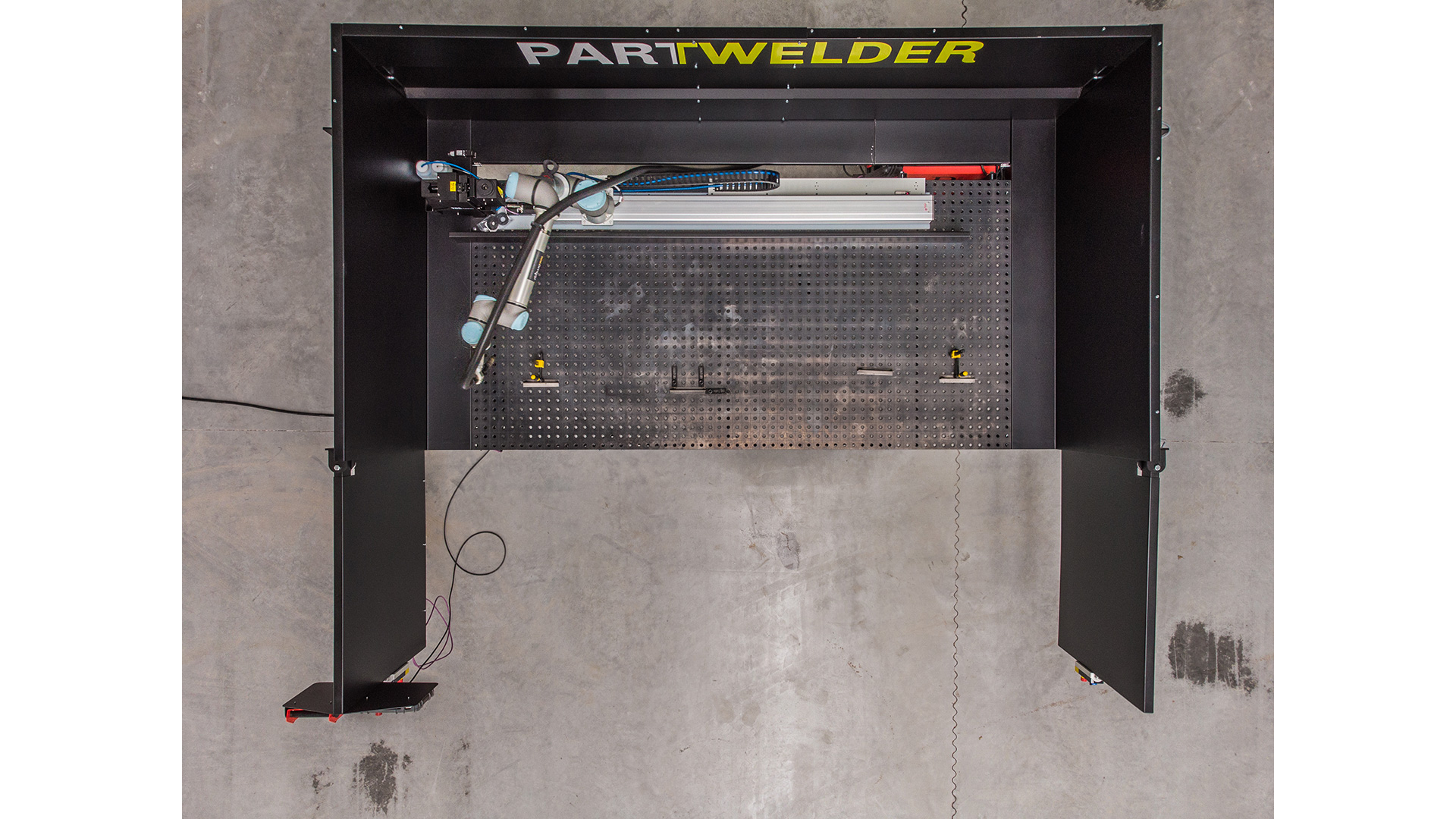
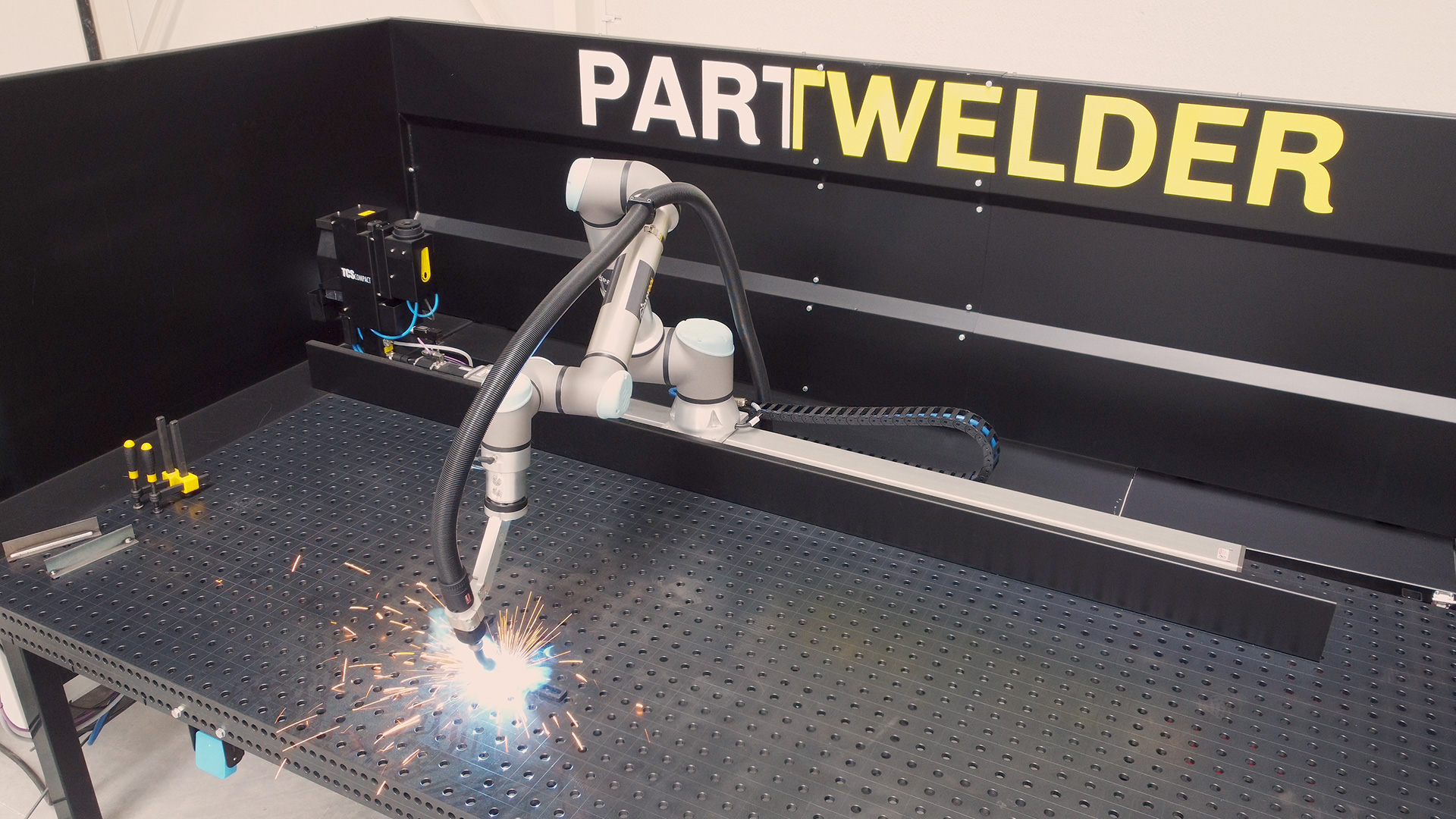
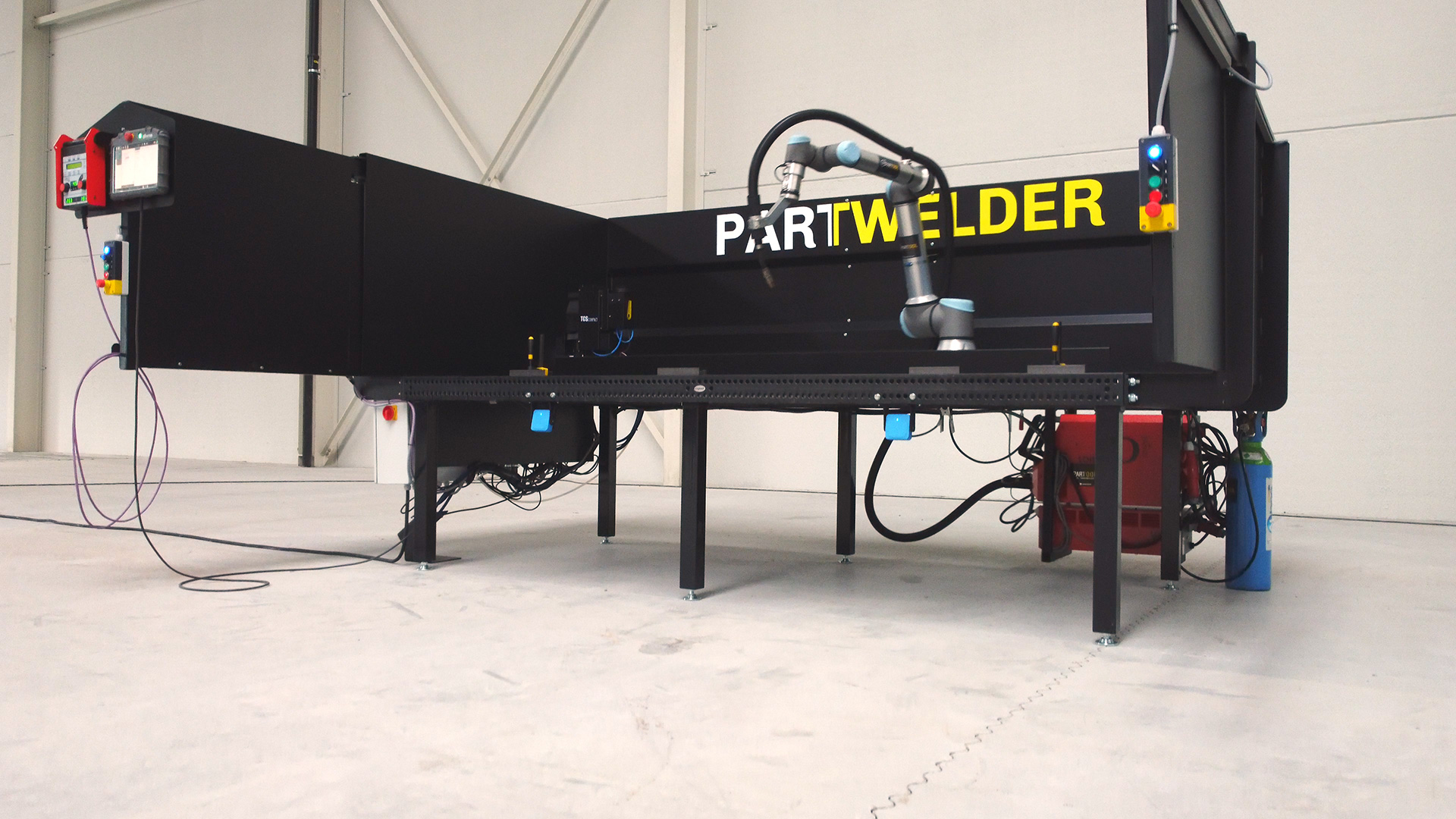
Introducing the Partwelder – a customised cobot welding system developed by Partool.
Cobots are robots that work alongside humans in the same environment. The cobot uses radar protection to ensure safety in the working environment. This ensures that when a human is working in the same environment, the cobot adjusts its speed to ensure a safer workplace.
"As the Universal Robots (UR) cobots have a limited working area, we were looking for a rail on which to place the cobots", says Koen Rosseel. "We found that Ewellix's SLIDEKIT made it possible to increase the cobot's working area and that it was a plug-and-play package. It is also straightforward to program the SLIDEKIT within the URcaps because Ewellix provides both the hardware and the software”.
Adding a linear module as a dynamic base for the cobot allows to extend its handling range, increasing productivity and output quality. SLIDEKIT 2.0 offers quick and easy installation thanks to a standardised mechanical, electrical and software interface with UR. As a result, the system is ready-to-use and can be programmed by the operator in just a few simple steps.
“The solution for our end customer is our PARTWELDER. This is a ready-to-use welding cell that is quick and easy to program. But the SLIDEKIT also has a working area of 3 m x 1.5 m, which is a great added value compared to other cobot setups without SLIDEKIT," says Koen Rosseel.
Electromechanical solutions offer improved machine performance and a larger work envelope for the cobot. For example, with the SLIDEKIT, the operator can copy the existing programme and have the same cobot reach an additional 200 mm simply by changing the position of the SLIDEKIT.
"Customers using our part welders have seen a 70% to 80% increase in output. In addition, the cobot can work faster and safer when there are no people at the table", explains Koen Rosseel.
Cobots combined with the SLIDEKIT 2.0 linear module provide a cost-effective solution for upgrading an existing assembly shop from a manual to a fully automated line.
Video
About Partool
In 1949, Vandenbulcke (later Partool) was founded in De Haan by André Vandenbulcke, specialising in drive and mechanical components. The company was later taken over by the father of our current director, Bernard Verhelst, after which Vandenbulcke moved to Ostend. The company has been active for over 70 years, specialising in drives and mechanical components. In the beginning it was a small company, but over time it has grown into a company with three divisions in Belgium: Ostend (head office), Ghent and Brussels. Today they are mainly involved in the supply and distribution of welding equipment for all industrial sectors.
Our products are used in thousands of industrial applications
Read more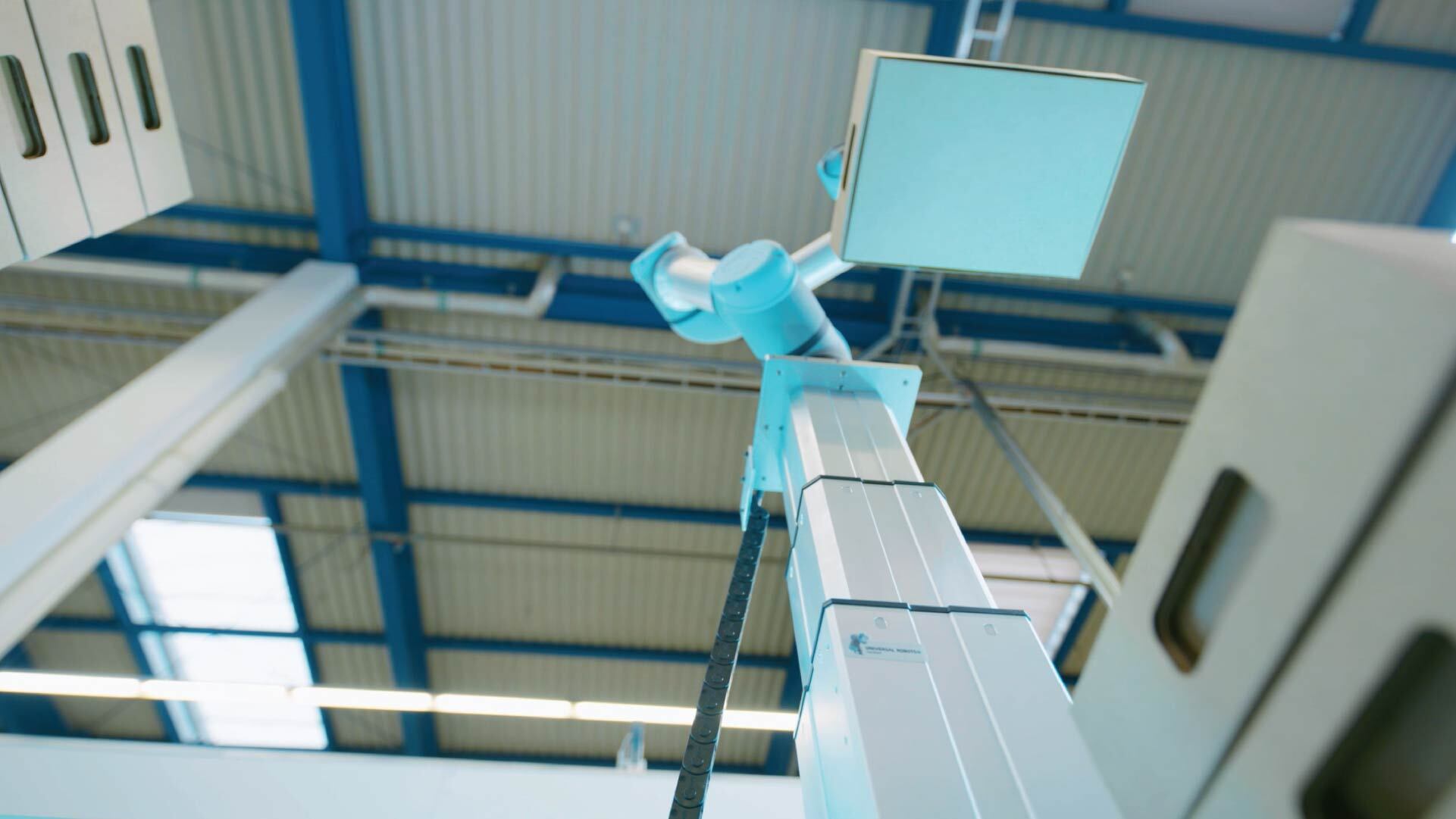
Need more
information?
Ask our experts.
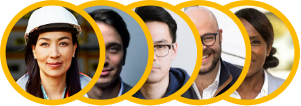